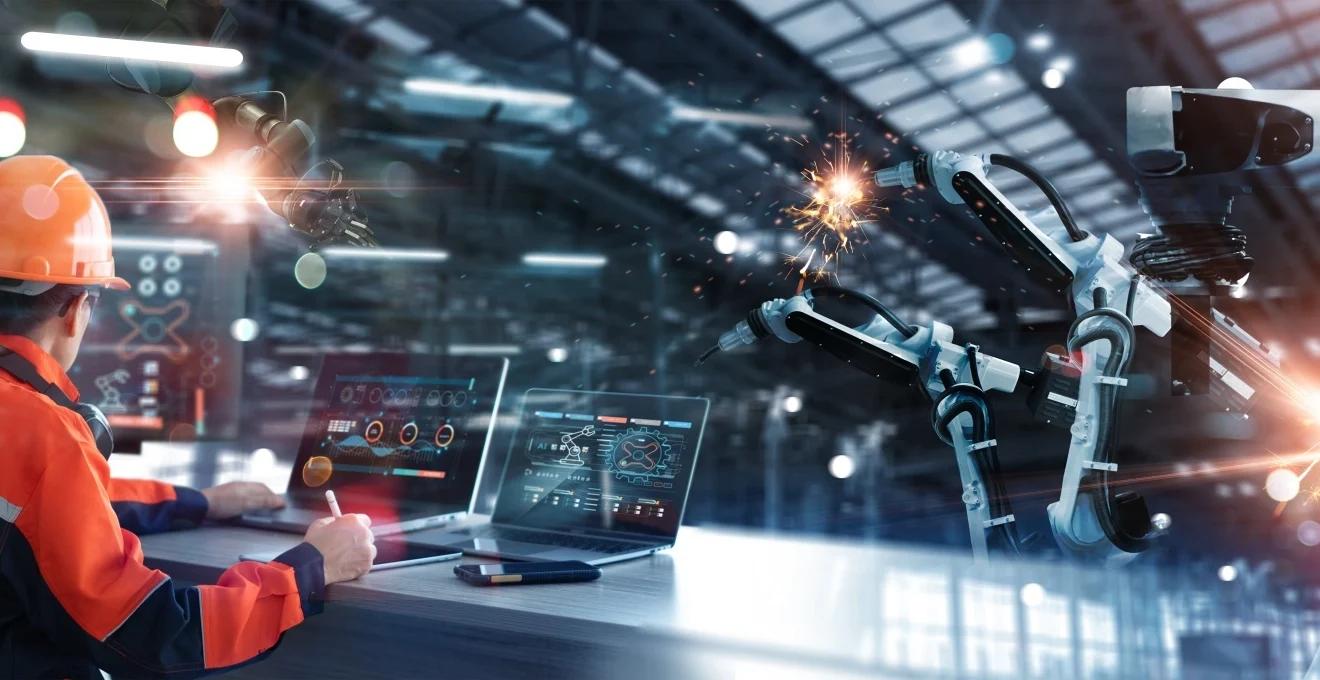
L'assemblage mécanique représente un pilier essentiel de l'industrie manufacturière moderne. Face à l'évolution rapide des technologies et des exigences du marché, les entreprises doivent constamment adapter leurs processus pour maintenir leur compétitivité. Cette dynamique soulève de nouveaux défis en termes de précision, d'efficacité et de flexibilité, tout en ouvrant la voie à des solutions innovantes qui redéfinissent les standards de l'industrie.
Dans un contexte où la personnalisation de masse et les cycles de production accélérés deviennent la norme, les techniques d'assemblage mécanique traditionnelles se trouvent parfois limitées. L'intégration de technologies avancées, telles que l'intelligence artificielle, la robotique collaborative et les systèmes de vision, offre de nouvelles perspectives pour surmonter ces limitations et propulser l'industrie vers de nouveaux sommets d'excellence opérationnelle.
Évolution des techniques d'assemblage mécanique dans l'industrie 4.0
L'avènement de l'industrie 4.0 a marqué un tournant décisif dans l'évolution des techniques d'assemblage mécanique. Cette nouvelle ère industrielle, caractérisée par l'interconnexion des systèmes et l'exploitation massive des données, a engendré une transformation profonde des processus de production. Les chaînes d'assemblage traditionnelles cèdent progressivement la place à des systèmes flexibles et intelligents, capables de s'adapter en temps réel aux variations de la demande et aux spécificités de chaque produit.
L'une des innovations majeures réside dans l'utilisation croissante de systèmes cyber-physiques. Ces dispositifs, alliant capteurs, actionneurs et intelligence embarquée, permettent une interaction sans précédent entre le monde physique de l'assemblage et l'environnement numérique de la gestion de production. Par exemple, des capteurs intégrés aux outils d'assemblage peuvent désormais collecter des données en temps réel sur la qualité des opérations, permettant des ajustements immédiats et une traçabilité accrue.
La digitalisation des processus d'assemblage ouvre également la voie à une personnalisation poussée des produits. Grâce à des systèmes de production modulaires et reconfigurables, les lignes d'assemblage peuvent rapidement s'adapter pour produire des séries limitées, voire des pièces uniques, sans compromettre l'efficacité globale. Cette flexibilité répond à une demande croissante de personnalisation de la part des consommateurs, tout en maintenant des coûts de production compétitifs.
L'assemblage mécanique moderne ne se contente plus de joindre des pièces ; il orchestre une symphonie complexe de données, de mouvements précis et d'intelligence artificielle pour créer des produits d'une qualité inégalée.
L'intégration de jumeaux numériques dans les processus d'assemblage représente une autre avancée significative. Ces répliques virtuelles des lignes de production permettent de simuler et d'optimiser les opérations avant leur mise en œuvre physique. Les ingénieurs peuvent ainsi tester différentes configurations d'assemblage, identifier les goulots d'étranglement potentiels et optimiser les flux de travail, le tout dans un environnement virtuel sécurisé.
Défis de précision et tolérances dans l'assemblage automatisé
L'automatisation croissante des processus d'assemblage mécanique soulève des défis considérables en termes de précision et de gestion des tolérances. À mesure que les composants deviennent plus complexes et les exigences de qualité plus strictes, la marge d'erreur acceptable se réduit considérablement. Cette réalité impose aux fabricants de repousser constamment les limites de la précision dans leurs opérations d'assemblage automatisé.
Un des principaux défis réside dans la variabilité inhérente aux composants mécaniques. Même avec les techniques de fabrication les plus avancées, de légères variations dimensionnelles sont inévitables. Ces écarts, bien que minimes, peuvent s'accumuler tout au long du processus d'assemblage, conduisant potentiellement à des défauts significatifs dans le produit final. Pour contrer ce phénomène, les industries adoptent des stratégies de compensation dynamique, où les systèmes d'assemblage s'ajustent en temps réel pour accommoder ces variations.
Systèmes de vision artificielle pour le contrôle dimensionnel
L'intégration de systèmes de vision artificielle dans les lignes d'assemblage représente une avancée majeure dans la quête de précision. Ces systèmes, équipés de caméras haute résolution et d'algorithmes sophistiqués de traitement d'image, permettent un contrôle dimensionnel en temps réel des composants et des assemblages. La capacité à détecter des écarts de l'ordre du micron offre un niveau de précision jusqu'alors inatteignable dans les processus d'assemblage à grande échelle.
Les systèmes de vision artificielle ne se limitent pas à la simple détection d'erreurs. Ils jouent un rôle proactif dans l'optimisation continue du processus d'assemblage. En analysant les tendances dans les variations dimensionnelles, ces systèmes peuvent identifier les sources récurrentes d'imprécision, permettant ainsi des ajustements préventifs des équipements ou des révisions des procédures d'assemblage.
Algorithmes d'ajustement dynamique pour la compensation des écarts
Face à la complexité croissante des assemblages mécaniques, les algorithmes d'ajustement dynamique deviennent indispensables. Ces outils logiciels sophistiqués analysent en temps réel les données collectées par les systèmes de vision et les capteurs intégrés aux équipements d'assemblage. Ils calculent ensuite les ajustements nécessaires pour compenser les écarts détectés, assurant ainsi que chaque opération d'assemblage respecte les tolérances spécifiées.
L'efficacité de ces algorithmes repose sur leur capacité à apprendre et à s'améliorer au fil du temps. En utilisant des techniques d'apprentissage automatique, ils affinent continuellement leurs modèles de prédiction, anticipant les variations potentielles et ajustant proactivement les paramètres d'assemblage. Cette approche prédictive minimise les rejets et optimise la qualité globale de la production.
Capteurs haptiques dans l'assemblage de composants sensibles
L'assemblage de composants sensibles ou fragiles pose des défis particuliers que les méthodes traditionnelles peinent à relever. L'intégration de capteurs haptiques dans les systèmes d'assemblage automatisé apporte une solution innovante à cette problématique. Ces capteurs, capables de mesurer avec une extrême précision les forces et les pressions appliquées, permettent un contrôle fin des opérations d'assemblage délicates.
Les capteurs haptiques trouvent une application particulièrement pertinente dans des domaines tels que l'électronique ou la micromécanique, où la manipulation de composants minuscules et fragiles est courante. En fournissant un retour tactile précis, ces capteurs permettent aux systèmes automatisés de réaliser des assemblages avec une délicatesse comparable à celle d'un opérateur humain expérimenté, tout en maintenant la rapidité et la répétabilité propres à l'automatisation.
Intégration des matériaux composites dans les processus d'assemblage
L'utilisation croissante de matériaux composites dans l'industrie manufacturière moderne présente à la fois des opportunités et des défis significatifs pour les processus d'assemblage mécanique. Ces matériaux, caractérisés par leur légèreté et leur résistance élevée, offrent des avantages considérables en termes de performance et d'efficacité énergétique. Cependant, leur nature complexe et hétérogène impose une refonte des approches traditionnelles d'assemblage.
L'un des principaux défis réside dans la jonction entre les composites et les matériaux métalliques traditionnels. Les différences de propriétés mécaniques et thermiques entre ces matériaux peuvent engendrer des contraintes localisées et des problèmes de durabilité à long terme. Pour surmonter ces obstacles, de nouvelles techniques d'assemblage hybride sont développées, combinant collage structural avancé et fixations mécaniques optimisées.
L'intégration de capteurs embarqués directement dans les structures composites ouvre de nouvelles perspectives pour le suivi en temps réel de l'intégrité des assemblages. Ces capteurs, souvent basés sur des technologies de fibre optique ou de nanotubes de carbone, permettent une surveillance continue des contraintes et des déformations au sein des structures assemblées, facilitant ainsi la maintenance prédictive et l'optimisation des performances sur le long terme.
L'assemblage de matériaux composites n'est pas simplement une évolution des techniques existantes, mais une révolution qui redéfinit les fondements mêmes de la conception et de la fabrication industrielle.
La conception pour l'assemblage (DFA - Design for Assembly
) prend une importance accrue dans le contexte des matériaux composites. Les ingénieurs doivent désormais intégrer les spécificités de ces matériaux dès les premières phases de conception, en tenant compte des contraintes liées à leur assemblage. Cette approche holistique permet d'optimiser non seulement la performance du produit final, mais aussi l'efficacité et la fiabilité du processus d'assemblage lui-même.
Optimisation des flux de travail et réduction des temps de cycle
Dans un contexte de concurrence mondiale accrue, l'optimisation des flux de travail et la réduction des temps de cycle deviennent des impératifs stratégiques pour les industries d'assemblage mécanique. Ces efforts d'amélioration continue visent non seulement à accroître la productivité, mais aussi à renforcer la flexibilité des chaînes de production face à une demande de plus en plus volatile et personnalisée.
L'adoption de méthodologies lean et agile joue un rôle central dans cette quête d'efficience. Ces approches, initialement développées dans l'industrie automobile, sont aujourd'hui appliquées avec succès dans divers secteurs de l'assemblage mécanique. Elles se concentrent sur l'élimination des gaspillages, la réduction des stocks intermédiaires et l'optimisation des flux de matériaux et d'information à travers l'ensemble du processus de production.
Analyse prédictive pour la maintenance préventive des équipements
L'analyse prédictive émerge comme un outil puissant pour optimiser la maintenance des équipements d'assemblage. En exploitant les données collectées par des capteurs IoT (Internet des Objets) intégrés aux machines, les algorithmes d'apprentissage automatique peuvent prédire avec précision les pannes potentielles avant qu'elles ne surviennent. Cette approche proactive permet de planifier les interventions de maintenance de manière optimale, réduisant ainsi les temps d'arrêt imprévus et maximisant la disponibilité des équipements.
Simulation numérique des processus d'assemblage complexes
La simulation numérique des processus d'assemblage complexes représente une avancée majeure dans l'optimisation des flux de travail. Grâce à des logiciels de CAE (Computer-Aided Engineering)
sophistiqués, les ingénieurs peuvent modéliser et simuler l'intégralité du processus d'assemblage avant même la mise en production. Cette approche permet d'identifier et de résoudre les problèmes potentiels dès la phase de conception, réduisant ainsi considérablement les temps et les coûts de développement.
Les simulations numériques offrent également la possibilité d'explorer rapidement différentes configurations d'assemblage et d'optimiser les séquences d'opérations. En intégrant des données réelles de production dans ces modèles numériques, les entreprises peuvent créer des jumeaux numériques de leurs lignes d'assemblage, permettant une optimisation continue et en temps réel des processus.
Systèmes de gestion lean pour l'efficacité opérationnelle
L'implémentation de systèmes de gestion lean constitue un levier puissant pour améliorer l'efficacité opérationnelle des processus d'assemblage mécanique. Ces systèmes, basés sur les principes du Toyota Production System, visent à créer un flux continu de valeur tout en éliminant systématiquement les gaspillages (muda
en japonais) sous toutes leurs formes.
L'utilisation d'outils lean tels que le kanban électronique, le SMED (Single-Minute Exchange of Die) pour la réduction des temps de changement de série, ou encore le Poka-Yoke pour la prévention des erreurs, permet d'optimiser significativement les flux de travail. Ces approches, combinées à une culture d'amélioration continue (Kaizen), créent un environnement propice à l'innovation et à l'efficience opérationnelle.
Robotique collaborative et sécurité dans l'assemblage mécanique
L'intégration de la robotique collaborative dans les processus d'assemblage mécanique marque une évolution significative vers des environnements de travail plus flexibles et plus sûrs. Contrairement aux robots industriels traditionnels, confinés derrière des barrières de sécurité, les robots collaboratifs, ou cobots, sont conçus pour travailler aux côtés des opérateurs humains, combinant la précision et l'endurance des machines avec la flexibilité et l'intelligence des humains.
Cette cohabitation homme-robot soulève néanmoins des questions cruciales en matière de sécurité. Les fabricants et les intégrateurs doivent s'assurer que l'introduction de cobots dans les lignes d'assemblage ne compromet en aucun cas la sécurité des travailleurs. Cela nécessite une approche holistique de la sécurité, intégrant à la fois des solutions technologiques avancées et une refonte des procédures de travail.
Protocoles de communication homme-machine en temps réel
L'efficacité de la robotique collaborative repose en grande partie sur la qualité de l'interaction entre l'opérateur humain et le robot. Les protocoles de communication en temps réel jouent un rôle crucial dans cette interaction, permettant un échange fluide et instantané d'informations. Ces protocoles doivent être à la fois robustes et intuitifs, capables de transmettre des instructions complexes tout en étant facilement compréhensibles par les opérateurs.
L'utilisation d'interfaces homme-machine (IHM) avancées, telles que les écrans tactiles et les systèmes de reconnaissance gestuelle, facilite cette communication. Par exemple, un opérateur peut utiliser des gestes intuitifs pour guider un cobot dans une tâche d'assemblage précise, le robot répondant immédiatement aux instructions. Cette approche permet une flexibilité accrue dans les processus d'assemblage, particulièrement utile pour les productions à faible volume ou hautement personnalisées.
De plus, l'intégration de technologies de réalité augmentée (RA) dans ces protocoles de communication ouvre de nouvelles perspectives. Les opérateurs peuvent visualiser en temps réel des informations superposées à leur environnement de travail, comme des instructions d'assemblage ou des alertes de sécurité, améliorant ainsi la précision et la sécurité des opérations.
Systèmes de détection de collision et d'arrêt d'urgence
La sécurité reste la priorité absolue dans tout environnement d'assemblage mécanique impliquant une collaboration homme-robot. Les systèmes de détection de collision et d'arrêt d'urgence constituent la pierre angulaire de cette sécurité. Ces systèmes utilisent une combinaison de capteurs avancés, tels que des capteurs de force, des caméras 3D et des scanners laser, pour créer une enveloppe de sécurité dynamique autour du robot.
En cas de détection d'une potentielle collision avec un opérateur ou un obstacle, ces systèmes peuvent déclencher un arrêt d'urgence en une fraction de seconde. Certains cobots sont même équipés de capteurs de couple sur chaque articulation, leur permettant de détecter le moindre contact imprévu et d'arrêter leur mouvement instantanément, avant même qu'une collision significative ne se produise.
L'intelligence artificielle joue un rôle croissant dans l'amélioration de ces systèmes. Des algorithmes d'apprentissage automatique peuvent analyser les schémas de mouvement des opérateurs et des robots, anticipant les trajectoires potentielles et ajustant dynamiquement les zones de sécurité. Cette approche proactive réduit considérablement le risque d'accidents tout en maximisant l'efficacité opérationnelle.
Ergonomie des postes de travail hybrides homme-robot
L'intégration de robots collaboratifs dans les environnements d'assemblage mécanique nécessite une réflexion approfondie sur l'ergonomie des postes de travail. L'objectif est de créer des espaces qui optimisent à la fois le confort et la productivité des opérateurs humains tout en facilitant une interaction fluide avec les cobots.
La conception de ces postes de travail hybrides doit prendre en compte les principes de l'ergonomie cognitive et physique. Par exemple, l'utilisation de stations de travail ajustables permet d'adapter la hauteur et l'orientation des surfaces de travail en fonction des tâches et des préférences individuelles des opérateurs. Cela réduit la fatigue et le risque de troubles musculo-squelettiques, problèmes courants dans les environnements d'assemblage traditionnels.
L'organisation spatiale des postes de travail joue également un rôle important. Une disposition bien pensée permet une transition fluide entre les tâches effectuées par l'humain et celles réalisées par le robot, minimisant les mouvements inutiles et optimisant le flux de travail. L'utilisation de systèmes de guidage visuel
, tels que des projecteurs laser ou des écrans intégrés, peut aider à diriger l'attention de l'opérateur vers les zones d'interaction importantes, réduisant ainsi la charge cognitive et améliorant l'efficacité.
L'ergonomie dans les environnements d'assemblage collaboratif ne se limite pas à la conception physique des postes de travail ; elle englobe également l'interface cognitive entre l'homme et la machine, créant un écosystème de travail harmonieux et productif.